

SOLAR AQUAPIRAMIDS FARMS
FUNDACION
AQUAPONIAS
DE VENEZUELA




THE SOLAR AQUAPIRAMIDS GREEN ECOSYSTEMS
COMPLEX

¨with 10 production units within two Solar Aquapiramids Naves, in less than 10 hectares, we can produce up to a little more than 5000 tons of vegetable per year and almost 400 tons of fish (tilapia), also produce up to 11,600 tons of organic green forage to rear 5.600 milking goats, lambs or 2000 cows or meat cattle and produce more than 8 million liters of organic goat milk or up to 1800 tons of cheese per year. On the other hand, with the traditional way of production it will be required up to over 3000 hectares of deforested forests for a similar production¨
Current events and evolution in the US and international markets has significantly determined the production and sales strategy that must be considered to face new trends and preferences of US consumers whiling to pay premium prices for locally grown fresh organic produces. These customers are eating more fresh every day. They also want ready-to-eat and better-for-their health, specialty cheeses, green organic grass-fed antibiotic and hormone-free natural proteins, deli and bakery goods and prepared foods, under a green natural concept of food production and food processing in bio-degradable, non-toxic packing. They want their products in the market quickly from production centers located close to where they are and access everything you can find in a regular supermarket but organic. Every traditional organic farmer and high-tech operation entrepreneurs are going for this market niche. However, if we see outside the box we’ll see that organic food stores such as Whole Food Market and supermarkets such as Wal-Mart also offer organic food in various finished value-added presentations with a net price difference with respect to fresh presentation up to 2.5 times higher while the investment required to give value-added represents pennies to a dollar. So who makes the big bucks in the food production industry, the farmers or the valued added manufacturing companies that produce products such as ketchup? Doing both may be the key strategy that we must establish to ensure a quick investment return and expansion in order to make the difference between an extraordinary success, a mediocre performance or total failure.
With an absolute independence from pollutant non-renewable conventional energy sources, maximizing the production efficiency by using less water, no non-renewable natural resources and a new operational and marketing strategy to increase profits, we will set the upscale environmental and economic feasibility of this proposals and constitute the starting point to reach the capacity to produce the food we will need in the next decades and beyond. Our determination for the excellence has resulted in a new innovated aquaponics system with controlled environment technologies and operational adaptations capable of executing tillage with accurate swiftness, performance and minimal operational personnel and new green, organic food technology processing systems for organic value-added products using no chemical preservatives and stabilizer and new green recyclable, non-toxic biodegradable and bio-plastics packing’s. Our goal is to offer everything you can find in a regular supermarket but in a green, organic and in bio-degradable and non-toxic packing presentation at accessible prices. This way our investors will to possess a unique competitive edge and advantage over the other companies to successfully penetrate a huge market niche in the growing organic food segment with quality, variety and prices lower than any competitors.

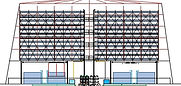


ZAYED AGRICULTURAL CENTER IN ABU DHABI, UNITES ARABS EMIRATES, CURRENTLY THE WORLD'S BIGGEST AQUAPONIC FARM (4000m2 OF GREENHOUSES)
This industry has been emerging in the last 20 years from small family farms to the biggest commercial operations represented by aquaponics complexes such as the Zayed Agricultural Center in Abu Dhabi, United Arabs Emirates, that with its 4000m2 of greenhouses and a production of over 200 tons of lettuces per year, is currently considered the world´s biggest farm with traditional aquaponics technology. And the vertical aquaponics operation by FarmedHere in Chicago, a Vertical Aquaponics Farm, winners of the 2013 Chicago Innovation Awards, due to the new value created for the end user, its market acceptance and its quantifiable evidence of success (http://www.chicagoinnovationawards.com/winners/up-and-comers/),
In a basic aquaponics system, effluents from the fish rearing tanks flow through filters that remove from the water suspended solids and gases released by food surplus and fish excretions decomposition, in order to flow through a hydroponic DFRT channels where dissolved nutrients are taken up by plants and ammonia and nitrites are removed by nitrifying bacteria growing on the sides of this channels, the underside
of the polystyrene sheets and the plants roots to recirculate clean water to be collected in a reservoir and returned to the rearing tanks, creating a close and perpetual re-circulation system.
This DFRT Hydroponic Channels are suitable for crops with roots that can tolerate a continuous flow of water through such as oregano or cilantro and hearty greens like Romaine, Watercress or Collard greens. These channels represent the crucial component of the Aquaponics System that provide the biological filtering and recirculation capacity that give this new food production concept its remarkable water saving characteristic (more than 96% of the water used in traditional agriculture) and an extremely high production yield.
However for crops like root vegetables, vine crops, raspberries/strawberries/blueberries, hot/sweet peppers, onions and garlic, that don’t need much water and in high humidity environments will be prone for roots to rotten and/or need a substrate medium for support a new type of hydroponic channel has been developed, Flow Substrate Bed Technic FSBT, which is an adaptation of the Bio-Filtering Substrate Gravel Bed Channels with flood & drain sub-irrigation that work interconnected and synchronized with the DFRT Channels systems in the Aquapiramides Units.
Also base on this new production concept a much wider production unit (Solar Aquapiramide) Nave has been developed as well combining synchronously in one section, the original Deep Flow Raft Technic, DFRT hydroponic Channels, conceived by James Rakosy at the University of the Virgin Islands and a Flow through Subtract Bed Technic FSBT hydroponic channel in the adjacent section.
Set at a pre-determine interval calculated for each crop, small amount of nutrient water solution coming from the Aquaponics’ degassed water tank in the Aquaponics’ filtering system are pump up to fill the FSBT channel and drained down by gravity into the next lower FSBT channel and keeps on going down by gravity to a reservoir where it is pump back to the DFRT Aquapiramide and up to the starting point at the most upper DFRT channels to undergo its regular filtering. This process keeps the medium regularly flushed with nutrients and air. The substrate made of gravel or clay granules provide the surface for nitrifying bacteria to flourish that turns ammonia in nitrogenous compounds that plants take to growth.
This new structural and production system concept makes this proposal unique and up to today the most advance Aquaponics Production system ever developed. It will allow to produce more than double the variety of items that the basic Aquaponics with hydroponic channels DFRT can produce, allowing to access new market niche giving it an unprecedented productive advantage
In the recirculating and continues reutilization of water processed, excecuted by all this production systems, both productions benefits and establish a successfully integration since plants growth rapidly with the rich nutrient effluents coming from the aquaculture tanks that accumulates in similar concentrations to the ones used in traditional hydroponics farming but would be contaminants capable to rising toxic levels in rearing tanks in traditional aquaculture. However in aquaponics this effluents serves as liquid fertilizer for the production beds where plants are raced hydroponically and in the process water is cleaned and returned to the rearing tanks.




The extraordinary feasibility of our concept and it's profitability as well as the relevant ecological characteristics rest on 5 determinant pillars:
1. When designing the Solar Aquapiramides of our Vertical Aquaponics Green Ecosystem we improved the structural concept of the vertical farms to increase the number and volume of aquaculture tanks and total lineal meters of hydroponic channels in less space thus in smaller buildings. We also designed an efficient filtering system to eliminate suspended solids in the water coming from the fish rearing tanks, capable of reducing, even more, the low water consumption of traditional aquaponics technology. We developed an efficient fish harvesting system for deep rearing tanks that can be operated by only two persons and execute harvesting in less time including also all the already proven state of the art technologies for controlled environment that has resulted in better quality and higher production rate with respect to already established enterprises.
2. Our designs follows the zero-waste and use criteria by combining technologies that indeed makes the difference with respect to other high tech aquaponics farms and establish its transcendental impact. We can recycle water, generates our electrical power by means of natural green unlimited sources, eliminating the use of local network and limits to what we can achieve and produce biochar (or bio-carbon), a by-product from our waste management system that a by-product from our waste management system that if added to 10% of the global cultivated lands could sequester the equivalent to 29 billions of CO2 (approximately equal to the annual greenhouse emissions generated by humanity) with positive effects in crops farmed in poor nutrient and depleted soils while creating the condition for reforestation to remove CO2 from the atmosphere, thus reverse global warming and climate change.

3.Unlike other aquaponics farms that concentrate its production strategies in producing only fresh produce, with little or no valued added, our Vertical Aquaponics Green Ecosystem will put more emphasis to the production of fresh produce as well. However since it has been conceived with Solar Aquapiramides as a production core for organic feedstock, it will also be surrounded by green eco-friendly food processing and valued added product manufacturing units to get the high profits potential of intermediary finished valued added products manufacturing companies but within an ecological concept with new green, organic food technology processing systems for organic value-added products using no chemical preservatives and stabilizer and new green recyclable, non-toxic biodegradable and bio-plastics packings. It will encourage the investment to reconvert traditional practices into more sustainable ones that with a global expansion will reach a profound change in the way we produce our food while eliminating the leading consumption of resources and most important, reversing the environmental degradation in our planet.
4. Furthermore, we have expanded our productive scope by including in our design a livestock forage production unit using an exceptional adaptation to recirculate water from the aquaculture tanks through an NFT (Nutrient Flow Technique) system for intensive livestock green forage production without the use of expensive liquid fertilizers to provide the pasture to feed milking goats and other livestock in closed controlled environment rearing units, keeping all year around the optimal environmental rearing conditions for the maximum production found in this animal’s place of origin. The combination of these previously describe systems, eliminates the need for deforesting 14 million hectares of forest every year and stops greenhouses gases, produced by animal agriculture (livestock and their byproducts).
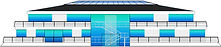

5. And we have achieved the capacity of obtaining the water we need from the humidity in the air, avoiding the intervention of naturals and man-made fresh water reservoir that must be reserved for human consumption as water availability becomes critical with population increase.

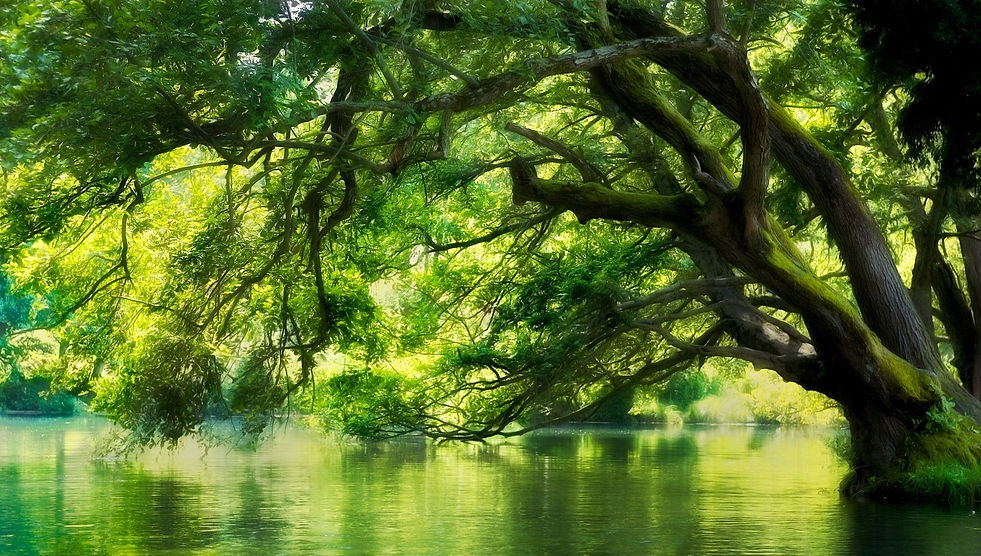
There are ways to replace our dependency to fossil fuels, though we won’t do that unless economics necessity demands it. But there isn’t a tidy and synthetic invention to replace water. We must reduce consumption and for years scientists had known that the extraordinary efficiency in saving water of the aquaponics technology (currently up to over 98% of the water required in traditional agriculture) represent a solution that has evolved thanks to the development of new designs and green technological adaptations conceived to reduce even more water consumption and to obtain it for agriculture with no intervention to man-made and natural reservoirs, exclusively reserved for human consumption due to population growth.
Every single component, from our core organic vegetables production units (Solar Aqauapiramides) and all the other structures to our water harvesting system from air, our harmful gasless AC system, our livestock rearing and green folder production system as well as all the processing and manufacturing lines has already been conceived and designed to every detail, pipes and power lines layouts, all the production and processing equipments, materials selections, and an operational logistic for a fast and simple construction as well as a for all the production aspects.
